3D Printing Has Finally Arrived
- Maria Inês Marreiros
- May 21, 2023
- 10 min read
Three-dimensional printing (3D printing), also known as additive manufacturing (AM) or rapid prototyping, is a quickly evolving technology that enables the creation of physical objects from a three-dimensional digital representation. It is referred to as additive because it does not require a block of material or mold to craft physical objects. Instead, 3D objects are created directly from a Computer-Aided Design (CAD) model. This CAD model can be constructed with design software or retrieved directly via reverse engineering processes. The latter process entails 3D scanning and measuring a physical object and then reconstructing it as a 3D model, i.e., the creation of a 3D model from an existing physical object (Harshavardhana, 2021). The foundational idea of 3D printing is the layer-by-layer construction of connected or solidified materials for the production of complex components (3D Printing Scales Up, 2013; Harshavardhana, 2021). Early 3D printing technologies started to emerge in the 1980s, with Charles W. Hull of 3-D Systems Corp. developing the first operational 3D printer in 1984 under the name "Stereolithography Apparatus" (Bogue, 2013). However, it took more than a decade for the technology to gain traction since it initially proved too costly for the general market. Originally, 3D printing technology was employed for constructing prototypes. However, as we arrived at the 21st century, its costs dropped dramatically, allowing 3D printers to find their way into a multitude of businesses. The 3D printer works similarly to a typical inkjet printer, except that instead of printing layers of ink on paper it uses materials to construct a three-dimensional object such as plastic (the most commonly used), metals, powders, resins, paper and even bio-inks, the latter consisting of materials used to produce artificially engineered living tissue (Attaran, 2017; Berman, 2012; Mahmood et al., 2022).
In the 20th century, Henry Ford invented the moving assembly line, which enabled identical objects to be mass-produced (The Moving Assembly Line and the Five-Dollar Workday, 2020). Currently, AM enables and streamlines the production of small to large quantities of customizable objects. Recent advances in materials, equipment, resolving capacity, computational speed, and accuracy have leveraged AM technology in multiple sectors. The benefits of such technology range from faster time-to-market of innovative designs, shorter manufacturing lead times, and faster fulfilment of customer requirements, bringing with it new production paradigms and manufacturing opportunities (Ntousia & Fudos, 2019). Car engines, personalized medicines, organs for transplants, food, clothing and even an entire city block can now be 3D printed. This raises the question of whether 3D printing is finally reaching its full potential.

3D Bioprinting: Shaping the Future of Medical Care
Breakthrough advances in technology and their application to human health have heralded a disruptive shift in the healthcare sector (Buonafede et al., 2018; Oliveira et al., 2020). This has led to a transition from a traditional medical paradigm toward a more personalized approach, the latter being heavily supported through the use of bioprinting. 3D bioprinting is the precise layer-by-layer deposition of biocompatible materials. So-called bioinks are hydrogels that are either naturally occurring, such as collagen or gelatin, or artificially produced hydrogels that are loaded with growth factors and living cells. While bioprinting builds on conventional 3D printing, it aims to create three-dimensional cell models and tissue constructs with the aim of mimicking natural tissue properties (Banerjee et al., 2022; Wu et al., 2022). The 3D bioprinting process typically begins with a sample of the patient's own cells being cultured and grown outside the body in a laboratory. These are then converted into a printable living ink, or bio-ink, consisting of a nutrient-rich media combined with hydrogel components. The bioink is then fed into a printing chamber to build tissue layer by layer (3D Bioprinting: Bioink Selection Guide, 2023). In modern medicine, bioprinting is a novel concept that can be used to manufacture skin, blood vessels or cartilage, entire organs such as the heart and liver (Garreta et al., 2017), as well as wearable monitoring sensors for disease diagnosis (Nasiri & Khosravani, 2020).
The lack of transplantable organs has become a public health crisis (Bastani, 2020). The overall number of patients on waiting lists greatly outnumbers the number of available donors. The challenges in transplantation are compounded by the fact that successful transplantation requires both acquisition of a healthy organ and management of complications such as infection and tissue rejection (Abbasov, 2022; Jiménez Oliver, 2023). 3D printed organs have advanced from the realm of science fiction to the edge of reality. Organovo was the first company to successfully commercialize 3D bioprints of human livers and kidneys in 2014 (Organovo Holdings, 2014). While bioprinted organs have the potential to transform transplantation and regenerative medicine, a plethora of scientific roadblocks stand in the way of the future. For instance, one of the most critical obstacles that still impedes its practical application is sustaining the functioning of complex organs over a long period of time, which in addition comes at a substantial cost (Barreiro Carpio et al., 2021; Rogers, 2023). Remarkably, last year, the first fully 3D bioprinted organ was successfully implanted in Texas. The patient's outer right ear was engineered to the size and shape of the left ear using the patient’s own cartilage cells (Rabin, 2022).

Another prominent example is Carcinotech, a firm focused on generating 3D printed tumor replicas to better understand and adapt cancer therapies. Using patient biopsy specimens, primary cells, immune cells, and cancer stem cells, Carcinotech delivers a platform for speedy, ethical, and accurate drug screening and customized drug testing. This allows for an assessment of treatment efficacy and toxicity on an individual basis. As a pioneer in the field of 3D-printed microtumors, the medical technology start-up aims to accelerate research on novel therapies and drugs that could help fight cancer and hence increase survival rates, while also offering personalized treatment for each cancer patient (Dorsey, 2022).
Overcoming the Housing Crisis with 3D Printing
The construction sector has not been spared from the disruptions that 3D printing is causing in several industries. The concept of 3D printed houses has been around for a while, but technology has only recently advanced enough to make it a viable option. With the help of nozzles and large 3D printers, foundations, walls, columns, stairs and other building components can be built layer by layer from concrete, plastic or other materials (McFadden, 2021). As a sustainable, cost-effective, and highly customizable alternative to conventional building techniques, 3D printed homes are redefining the way we think about home construction. As the construction sector faces uncertain times owing to a scarcity of qualified labor, rising costs, and worldwide housing shortages, the new digital and sustainable possibilities of additive manufacturing are proving to be real game changers. Not only is the construction time shortened, which leads to lower costs, but environmental benefits are also notable: 3D printed houses are considered the future of environmentally friendly house construction. This greener method generates about 30% of the waste generated by traditional construction. Furthermore, the cement mixture used in 3D printers may be manufactured from recycled plastic and other long-lasting eco-friendly materials (Azcárate, 2023). However, 3D printing is currently restricted to the building framework. Therefore, conventional construction techniques must still be used to set up components such as windows, electricity and plumbing. Nonetheless, attempts are underway to develop fully functional printing software with extensive mechanical, electrical and plumbing components.
The last few years were marked not only by the construction of 3D printed houses, but also by the approval of projects for entire neighborhoods. BioHome3D is the world's first 3D printed house composed entirely of biodegradable and recyclable materials. The 600-square-meter house was produced layer by layer using an industrial 3D printer and no concrete. Instead, biomaterials, such as wood fiber flour and sawdust, were combined with bioresin and corn (BioHome3D, 2022). The house was created last year at the Advanced Structures and Composites Center at the University of Maine using the world's largest polymer 3D printer. It features 3D printed floors, walls and roof, is highly insulated and equipped with thermal, environmental and structural sensors to monitor how BioHome3D performs in frigid climates (Burgos, 2023).

Following the small-scale debut of the 3D printing housing industry, the first 50-home village was 3D printed in Nacajuca, Mexico, in 2020. Each residence in the community is hurricane- and earthquake-proof (Saxton, 2020). Notably, Nacajuca was struck by a 7.4 magnitude earthquake shortly after the structures were built, yet the residences were unscathed. Three organizations worked together to create this 3D printed village: New Story, a non-profit dedicated to reducing homelessness, ICON, a building technology company dedicated to improving housing, and CHALE, a non-profit partner in Mexico, which focuses on affordable housing (Papadopoulos , 2021). This endeavor is part of New Story's exploration of construction technologies that could help in the provision of affordable homes for the world's poorest regions.
Completed earlier this year near Austin, Texas, “The Genesis Collection”, a 100-home addition to Wolf Ranch's projected 2,500 houses, is the world's largest 3D printed community. Lennar Corp, the second-largest house builder in the United States cooperated with ICON to achieve such a key milestone in the history of 3D printed home construction (Woody, 2023). Houses were printed using ICON's first-generation Vulcan printer, a 46.5-foot-wide robot with an oscillating crossbar and attached nozzle that extrudes "Lavacrete", an ICON-developed proprietary material that is highly printable and incredibly durable (Vulcan Construction System, n.d.). Scalable 3D printing holds the potential of building waste-free, inexpensive, and energy-efficient houses with unique designs and at a much faster pace.

Designing a Masterpiece: The Era of Edible Prints
Most people are familiar with the "Replicator", Star Trek's food machine that can convert any molecule into delicious food and healthy meals. 3D food printing seems to bring us closer to the sci-fi ideal, making it possible to create meals from a range of pastes and materials. 3D food printing is a breakthrough technology that has the potential to improve the nutritional value of meals and reduce famine in countries where nutritious and affordable ingredients are limited (H. Rogers & Srivastava, 2021). A food 3D printer is comprised of a stainless-steel nozzle or cartridge that extrudes edible, food-safe materials such as chocolate, cookie dough, cheese, icing, mousse, and even raw meat (Hao et al., 2010; Sun et al., 2020). These are heated and applied layer by layer to a plate or other surface with robotic precision, much like icing a cake with a piping bag (Beecher, 2022). An advantage over mass-produced meals is the ability to customize the taste and texture of 3D-printed foods by altering the spatial distribution of flavoring components while controlling geometric patterns. The ability to dynamically change the color, shape and flavor of 3D printed meals has recently been made possible by 4D food printing technologies (Derossi et al., 2021; Zhu et al., 2020). The latter includes smart design and smart materials that allow 4D printed objects to change form or function, yet such technology is currently not readily accessible due to the heavy costs (Bashir et al., 2022). Because of the variety and affordability of food 3D printers and materials available on the market, today's high-end restaurants are able to offer a unique, fully personalized dining experience. Large food producers have likewise profited from the use of 3D printing. Pasta manufacturer Barilla, for example, is a pioneer in 3D printed pasta and now has 15 different shapes from the “BluRhapsody” collection on the market (Wakefield, 2022).
Chocolate has been successfully 3D printed in the food industry due to its popularity and natural physical properties, such as low melting temperature and solidification at ambient temperature, (Liszewski, 2022). The first 3D printing studio capable of mass-producing chocolate was built in 2020 by the Barry Callebaut Group, a leading manufacturer of high-quality chocolate and cocoa products. The company's crowning achievement, 'Flore de Cacao', is a one-of-a-kind 3D-printed chocolate sculpture that opens like a flower when hot chocolate is poured inside (Griffiths, 2020). Another notable material in the field of 3D food printing is sugar, a pliable substance that can take different shapes and colors and is also compatible with 3D printing. Some companies, such as the CandyFab Project and 3D Systems Sugar Lab, have developed 3D printers that specialize in producing sugar and candies in distinctive 3D designs (Anusci, 2015). To push the boundaries of 3D printing even further, scientists are currently 3D printing meat using biomaterials and animal stem cells. Surprisingly, some 3D printed meats are made from plant-based ingredients like soy, pea protein, beetroot, chickpeas, and coconut oil, and still taste like meat (Patel, 2021).
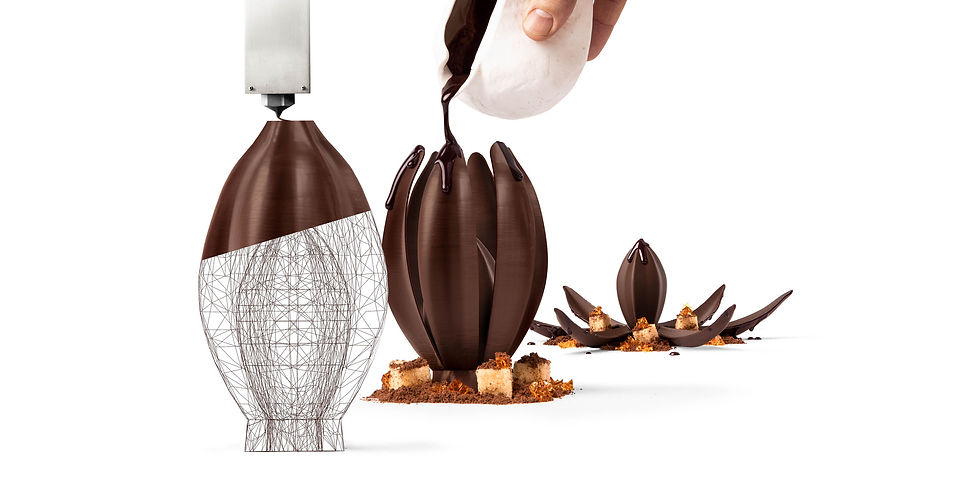
It's no surprise that food safety is the number one concern with the adoption of 3D printing in the food industry. 3D printing technology manufactures food in a very short period of time, which eventually restricts food cooking at certain temperatures or might cause shifts in temperature that promote the growth of hazardous pathogens. Furthermore, the print is not food safe since even the smoothest prints have tiny breaks and gaps between layers that allow microbes to thrive. To minimize contamination-related issues, food preparation manufacturers must follow a variety of established standards and regulations, including the coating of 3D printed products with food-safe resins. Additionally, not all components used in traditional cooking may be used by 3D printed food manufacturers, and each component has specific storage and processing requirements (The Essential Guide to Food Safe 3D Printing: Regulations, Technologies, Materials, and More, 2023)
Conclusion
The concept of 3D printing was first introduced in science fiction literature in the 1950s and finally became a reality in the 1980s. The basic ideas are still valid today: An object is digitally built up layer by layer. 3D printing has evolved significantly over the past 30 years and now plays a multidimensional role in every industry, with the potential to revolutionize society and have a positive impact. When 3D printing first gained widespread recognition in 2010, it was heralded as a consumer technology. Every household would have a 3D printer that could produce everything from consumer clothing to food. However, 3D printing has evolved into a much more dynamic technology, responding to societal demands rather than individual customer needs. There are a variety of uses for 3D printing, including making complex orthopedic implants or organs for transplants, designing sustainable homes or villages, preparing special meals for specific dietary needs, and making car and airplane parts. The use of recyclable and biodegradable components makes 3D printing a more environmentally friendly production technique, despite the significant energy consumption. However, cybersecurity risks are a reality. Being entirely digital, 3D items are an attractive target for hackers who might alter print file instructions or steal product designs. It is not difficult to understand how dangerous this can be when, for example, medicines or military weapons are manufactured using 3D technology. It won't be long before 3D printing replaces traditional production techniques. Therefore, it is crucial to understand the dangers posed by this technology. Throughout human history, there have been several times when technology has fundamentally changed the way people live, from cell phones to personal computers. With the advent of 3D printing, we are undoubtedly in one of those times.
Bibliographical References
3D Bioprinting: Bioink Selection Guide. (2023). Merck. https://www.sigmaaldrich.com/ES/es/technical-documents/technical-article/cell-culture-and-cell-culture-analysis/3d-cell-culture/3d-bioprinting-bioinks
3D printing scales up. (2013). The Economist. https://www.economist.com/technology-quarterly/2013/09/05/3d-printing-scales-up
Abbasov, I. B. (2022). Three-Dimensional Bioprinting of Organs: Modern Trends. Critical Reviews in Biomedical Engineering, 50(3), 19–34. https://doi.org/10.1615/CritRevBiomedEng.2022043734
Anusci, V. (2015). Food 3D Printing Starts from the Sweet Ending. All3DP. https://all3dp.com/food-3d-printing-starts-sweet-ending/
Attaran, M. (2017). The rise of 3-D printing: The advantages of additive manufacturing over traditional manufacturing. Business Horizons, 60(5), 677–688. https://doi.org/10.1016/j.bushor.2017.05.011
Azcárate, M. (2023). Are 3D Printed Houses The Future Of Home Building? The next Cartel. https://thenextcartel.com/discover/are-3d-printed-houses-the-future-of-home-building/
Banerjee, D., Singh, Y. P., Datta, P., Ozbolat, V., O’Donnell, A., Yeo, M., & Ozbolat, I. T. (2022). Strategies for 3D bioprinting of spheroids: A comprehensive review. Biomaterials, 291, 121881. https://doi.org/10.1016/j.biomaterials.2022.121881
Barreiro Carpio, M., Dabaghi, M., Ungureanu, J., Kolb, M. R., Hirota, J. A., & Moran-Mirabal, J. M. (2021). 3D Bioprinting Strategies, Challenges, and Opportunities to Model the Lung Tissue Microenvironment and Its Function. Frontiers in Bioengineering and Biotechnology, 9. https://doi.org/10.3389/fbioe.2021.773511
Bashir, B., Reshi, M., & Akeemu, Q. (2022). 4D Printing in Food Technology: Way to Sustainable Growth. Food Infotech. https://www.foodinfotech.com/4d-printing-in-food-technology-way-to-sustainable-growth/
Bastani, B. (2020). The present and future of transplant organ shortage: some potential remedies. Journal of Nephrology, 33(2), 277–288. https://doi.org/10.1007/s40620-019-00634-x
Beecher, C. (2022). 3D food printers are already a science fact, not far-fetched science fiction. Food Safety News. https://www.foodsafetynews.com/2022/10/3d-food-printers-are-already-a-science-fact-not-far-fetched-science-fiction/
Berman, B. (2012). 3-D printing: The new industrial revolution. Business Horizons, 55(2), 155–162. https://doi.org/10.1016/j.bushor.2011.11.003
BioHome3D - Advanced Structures & Composites Center. (2022). The University of Maine. https://composites.umaine.edu/biohome3d/
Bogue, R. (2013). 3D printing: the dawn of a new era in manufacturing? Assembly Automation, 33(4), 307–311. https://doi.org/10.1108/AA-06-2013-055
Buonafede, F., Felice, G., Lamperti, F., & Piscitello, L. (2018). Additive Manufacturing and Global Value Chains: An Empirical Investigation at the Country Level. In Progress in International Business Research. (pp. 295–323). Emerald Publishing Limited. https://doi.org/10.1108/S1745-886220180000013013
Burgos, M. (2023). World’s first 100% bio-based 3D-printed home in maine is built with sawdust and corn. Designboom. https://www.designboom.com/architecture/biohome3d-3d-printed-bio-based-university-of-maine-01-06-2023/w burgos
Derossi, A., Caporizzi, R., Paolillo, M., Oral, M. O., & Severini, C. (2021). Drawing the scientific landscape of 3D Food Printing. Maps and interpretation of the global information in the first 13 years of detailed experiments, from 2007 to 2020. Innovative Food Science & Emerging Technologies, 70, 102689. https://doi.org/10.1016/j.ifset.2021.102689
Dorsey, K. (2022). Carcinotech lands seven-figure funding deal to take on cancer. Herald Scotland. https://www.heraldscotland.com/business_hq/20092687.carcinotech-lands-seven-figure-funding-deal-take-cancer/
Garreta, E., Oria, R., Tarantino, C., Pla-Roca, M., Prado, P., Fernández-Avilés, F., Campistol, J. M., Samitier, J., & Montserrat, N. (2017). Tissue engineering by decellularization and 3D bioprinting. Materials Today, 20(4), 166–178. https://doi.org/10.1016/j.mattod.2016.12.005
Griffiths, A. (2020). Barry Callebaut 3D-prints intricate desserts in Belgian chocolate. Dezeen. https://www.dezeen.com/2020/03/21/3d-printing-chocolate-barry-callebaut/
Hao, L., Mellor, S., Seaman, O., Henderson, J., Sewell, N., & Sloan, M. (2010). Material characterisation and process development for chocolate additive layer manufacturing. Virtual and Physical Prototyping, 5(2), 57–64. https://doi.org/10.1080/17452751003753212
Harshavardhana, N. (2021). Review on 3D printing of medical parts. Additive Manufacturing, 63–84. https://doi.org/10.1016/b978-0-12-822056-6.00005-9
Jiménez Oliver, K. (2023). Overview of Organ Donation. Mexican Journal of Medical Research ICSA, 11(21), 55–63. https://doi.org/10.29057/mjmr.v11i21.10007
Liszewski, A. (2022). Scientists Say They’ve Created Crispier Chocolate Using 3D Printers. Gizmodo. https://gizmodo.com/3d-printed-chocolate-has-more-snap-crisp-texture-1848829608
Mahmood, A., Akram, T., Chen, H., & Chen, S. (2022). On the Evolution of Additive Manufacturing (3D/4D Printing) Technologies: Materials, Applications, and Challenges. Polymers, 14(21), 4698. https://doi.org/10.3390/polym14214698
McFadden, C. (2021). 7 of the most beautiful 3D-printed houses and cabins. Interesting Engineering. https://interestingengineering.com/innovation/7-of-the-most-beautiful-3d-printed-houses-and-cabins
Nasiri, S., & Khosravani, M. R. (2020). Progress and challenges in fabrication of wearable sensors for health monitoring. Sensors and Actuators A: Physical, 312, 112105. https://doi.org/10.1016/j.sna.2020.112105
Ntousia, M., & Fudos, I. (2019). 3D Printing Technologies & Applications: An Overview. Proceedings of CAD’19, 243–248. https://doi.org/10.14733/cadconfP.2019.243-248
Oliveira, J. P., Santos, T. G., & Miranda, R. M. (2020). Revisiting fundamental welding concepts to improve additive manufacturing: From theory to practice. Progress in Materials Science, 107, 100590. https://doi.org/10.1016/j.pmatsci.2019.100590
Organovo Holdings. (2014). Organovo Celebrates a Positive 2014 Reception of its exVive3DTM Human Liver Tissue Product. Cision. https://www.prnewswire.com/news-releases/organovo-celebrates-a-positive-2014-reception-of-its-exvive3dtm-human-liver-tissue-product-300009373.html
Papadopoulos, L. (2021). This Entire Village Was Built By a Single 3D Printer. Interesting Engineering. https://interestingengineering.com/innovation/this-entire-village-was-built-by-a-single-3d-printer
Patel, P. (2021). Beyond Burgers: Animal and Plant Cells Combined for 3D-Printed Steaks. IEEE Spectrum. https://spectrum.ieee.org/3d-printed-meat#toggle-gdpr
Rabin, R. C. (2022). Doctors Transplant Ear of Human Cells, Made by 3-D Printer. The New York Times. https://www.nytimes.com/2022/06/02/health/ear-transplant-3d-printer.html
Rogers, H., & Srivastava, M. (2021). Emerging Sustainable Supply Chain Models for 3D Food Printing. Sustainability, 13(21), 12085. https://doi.org/10.3390/su132112085
Rogers, K. (2023). When we’ll be able to 3D-print organs and who will be able to afford them. CNN Health. https://edition.cnn.com/2022/06/10/health/3d-printed-organs-bioprinting-life-itself-wellness-scn/index.html
Saxton, M. (2020). 3D-Printed Homes and Neighborhoods. Build With Rise. https://www.buildwithrise.com/stories/3d-printed-homes-and-neighborhoods
Sun, Y., Zhang, M., & Chen, H. (2020). LF-NMR intelligent evaluation of rheology and printability for 3D printing of cookie dough pretreated by microwave. LWT, 132, 109752. https://doi.org/10.1016/j.lwt.2020.109752
The Essential Guide to Food Safe 3D Printing: Regulations, Technologies, Materials, and More. (2023). FormLabs. https://formlabs.com/blog/guide-to-food-safe-3d-printing/
The moving assembly line and the five-dollar workday. (2020). Ford Corporate. https://corporate.ford.com/articles/history/moving-assembly-line.html
Vulcan Construction System. (n.d.). ICON. https://www.iconbuild.com/technology
Wakefield, E. (2022). BluRhapsody 3D printed pasta by Barilla now available to buy. Voxel Matters. https://www.voxelmatters.com/3d-printed-pasta-created-by-barillas-blurhapsody-in-italy-of-course/
Woody, T. (2023). The world’s largest 3D-printed neighborhood is here. Bloomberg. https://www.bloomberg.com/features/2023-3d-printed-houses-austin-texas/
Wu, Y., Fuh, J., & Ozbolat, I. T. (2022). 3D Bioprinting in Tissue and Organ Regeneration. In Elsevier. https://www.sciencedirect.com/book/9780128242919/3d-bioprinting-in-tissue-and-organ-regeneration?via=ihub=
Zhu, S., Ribberink, M., de Wit, M., Schutyser, M., & Stieger, M. (2020). Modifying sensory perception of chocolate coated rice waffles through bite-to-bite contrast: an application case study using 3D inkjet printing. Food & Function, 11(12), 10580–10587. https://doi.org/10.1039/D0FO01787F
Visual Sources
3D printing has become a new hobby for me, because the possibilities for creating things from scratch are endless. But even in the most creative moments, you need to relax. I recently discovered the casino at https://luckystaronlinecasino.in/, and it has been a great way to unwind after hours of working with the printer. The casino offers a variety of games, exciting bonuses, and a sense of excitement that is reminiscent of the thrill of a successful print. If you love 3D printing and are looking for something to diversify your leisure time, this casino will definitely appeal to you!